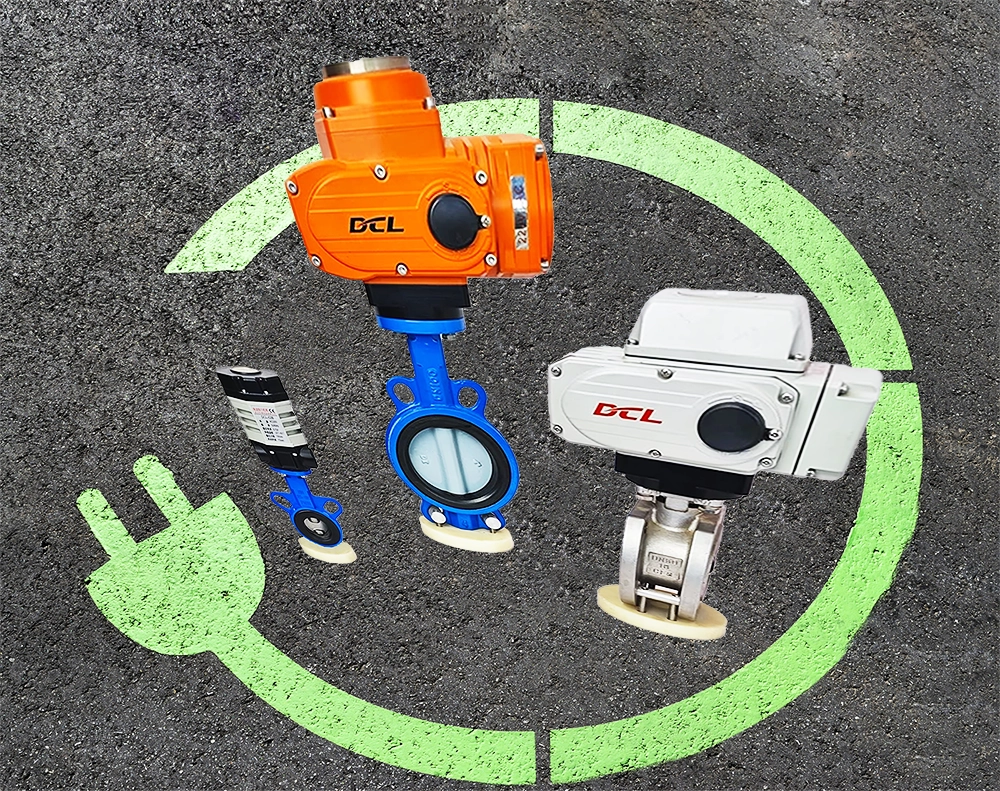
Electric actuators utilize the technical method of motor-driven deceleration mechanism to realize rotary and linear movements of valves. Because they are motor-driven, electric actuators are simple and reliable, and do not require additional supporting facilities such as pneumatic and hydraulic sources. This means more efficient energy utilization and lower cost of ownership. At the same time, higher reliability and a longer service life are achieved. Precise, fast and complex valve movements can be realized by using electronic control modules to drive electric actuators. Therefore, fluid control applications can be realized with higher precision, faster response and higher efficiency using electric actuators.
reliable and durable
The electric actuator has a simple structure and is more reliable and durable.Electric motors, as non-contact motion devices, generate much less mechanical wear in the work engineering than devices such as cylinders, which rely on mechanical friction motion. At the same time, electric motors do not have the requirement of airtightness and are more tolerant to mechanical wear. Under the same wear and tear, electric motors can work normally, while cylinders may lose their function completely due to air leakage. Therefore, electric actuators are more reliable and durable and can be adapted to more application scenarios.
compact
Electric actuators have a simple structure and compact size. In shipboard, vehicle, train, aviation and other fluid control equipment, because the installation volume is limited, often only compact structure, small size of the electric actuator.
high efficiency
Electric actuators are more efficient, saving more than 60% of energy, theHigher efficiency means lower costs and fewer carbon emissions.First of all, electric actuators do not require the use of an air source, which alone can save more than 60% of energy. This is because we know that the efficiency of an air compressor is just over 30%, while the transmission efficiency of low-power electricity is close to 100%. In addition, if we consider the leakage of the air circuit and the unwanted pressure released into the environment when the pneumatic device releases pressure, the electric actuator will save even more energy.
Controllability + High Precision
Electric actuators are more controllable and more precise in their control. The control module allows precise control of the motor's motion parameters, including speed and output torque. Special functions such as soft start, variable speed, constant torque output, and anti-surge can also be realized for specific fluid control applications.
usability
Electric actuators are easier to use and have a wider range of applications, you can use them in almost any situation that is not an oversized fluid control loop.By connecting the power supply from the site to the electric actuator in situ, you can drive the valve and realize fluid control. You don't need to configure ancillary facilities such as a pneumatic or hydraulic source for the electric actuator, and you can also eliminate the need to deploy pneumatic and hydraulic circuit engineering. Of course, the maintenance of the power supply is also much simpler than that of the pneumatic and hydraulic sources.
DCL electric actuator
DCL electric actuators focus on reliability and durability. Through the design of ultra-resistant tooth, wide frequency domain immunity and fully encapsulated control unit, DCL electric actuators are widely used in harsh environmental working conditions. DCL electric actuators have accumulated reliable and durable application experience in electromagnetic harsh working conditions such as base stations, extra high voltage, strong radiation, and in harsh environments such as offshore, high humidity, salt spray, dust, and strong temperature difference.
With the optional Huayi ZhiControl Industrial Internet of Things (IoT) feature options, DCL electric actuators also enable wide-area fluid control, actuator self-diagnostics, life prediction and advance maintenance. These features can help protect you from the hassle and financial loss of stopping a critical fluid control process.